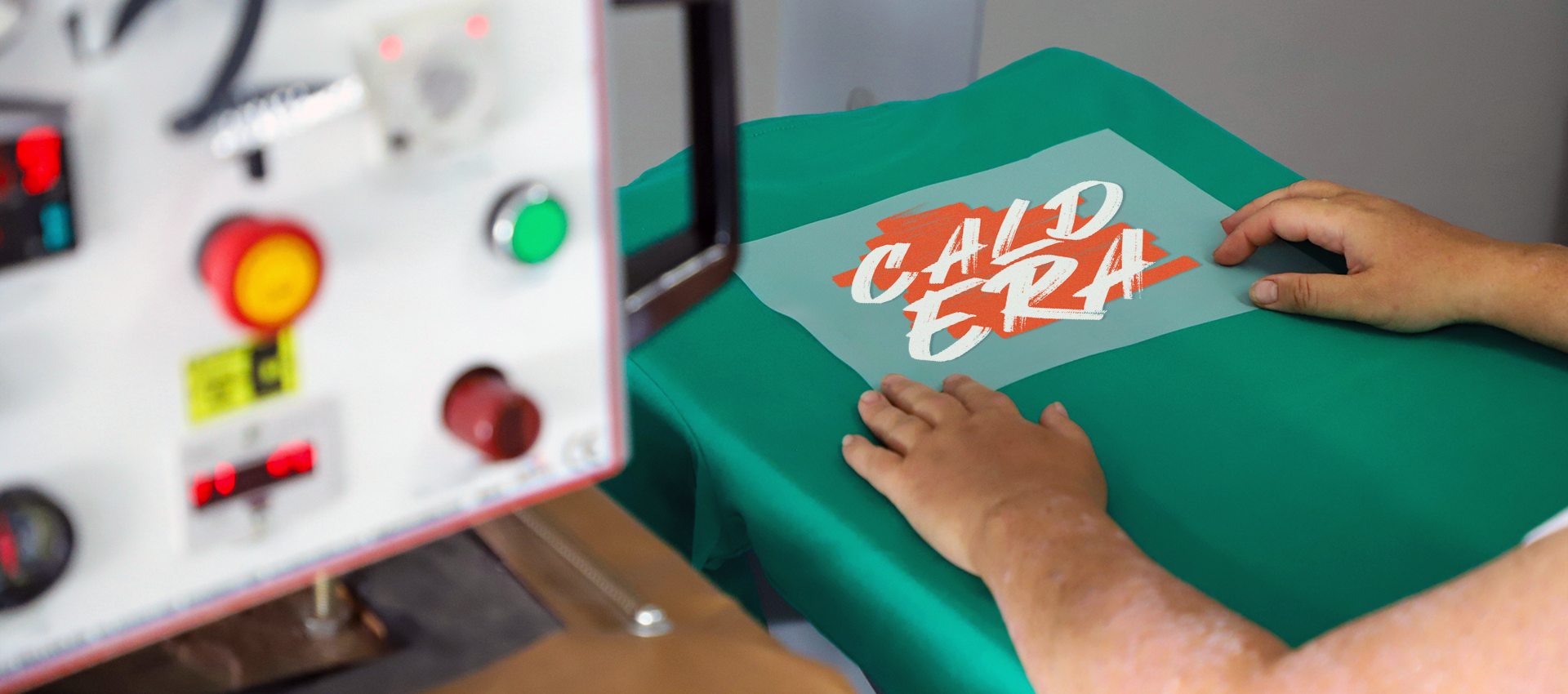
Why DTF print shops can’t afford to ignore Caldera PrimeCenter
April 22, 2025
PrimeCenter is a nesting and job preparation software that makes a real difference in workflow efficiency across a wide range of printing applications. But it truly excels in one area: DTF. We spoke with Joey Phillips, Caldera’s Global Technical Sales Manager, to learn why it’s such a perfect match.
With a tendency to multiple small and unique jobs in the DTF workflow, there are a number of different ways that PrimeCenter works well in this complex print environment. Joey explains: “I think the first one is with PrimeCenter’s ability to generate print-ready PDFs and cut files for use with any cutter on the market. PrimeCenter has the ability to seamlessly prepare transfers from artwork files through to garment-ready.”
One thing that DTF print operators find really useful is a capability to add tear-off annotations. It’s a powerful way to match transfers to precisely the right garment – something that’s been a big gap in the market up to now. “You don’t want to have to print job names or numbers as part of the transfer and have them ending up on the garment,” says Joey. “So with PrimeCenter, we can actually add metadata underneath each transfer, add a cut path to it, but also make it so that tear off annotation can be easily removed when it’s married up with the correct garment at the heat press.” In other words, you have excellent tracking visibility for every piece, combined with a streamlined workflow that’s super easy to implement.
How can you tell if PrimeCenter fits your operation?
While your first concern might be whether PrimeCenter would work with your RIP, there’s no need to worry. Virtually all the DTF RIPs on the market support PDF cut files, which means you can use PrimeCenter whether you use Caldera or an alternative RIP.
“What I usually like to ask,” says Joey, “is what type of jobs do you produce? A lot of one-offs or hundreds of the same artwork? If you’re doing 100s that are all the same, the tear-off annotations aren’t a huge benefit, though the nesting and cutting still can be. So I like to understand the dynamics of the workflow in terms of numbers of pieces. Also how you’re receiving the orders can be vital information for workflow discussion. It’s important to know what type of cutting hardware and capabilities there are. Some printshops are introducing DTF specific cutters, and we can implement PrimeCenter to work with these.”
PrimeCenter also helps eliminate common workflow bottlenecks, such as files arriving on oversized art boards that waste both media and time.
PrimeCenter’s five big benefits
Caldera has identified five ways in which PrimeCenter offers significant benefits to your workflow:
- time savings
- maximization of material yields
- error elimination
- workflow optimization
- simplified file preparation
DTF printers can build advantage in all these areas by using PrimeCenter. Joey talks about workflow optimization and file preparation: “What’s amazing about PrimeCenter is that it can actually use metadata directly from the file name. For example, the number of copies can be extracted from the file name, as well as the order ID and the sequencing for printing and cutting. This means you can control the workflow to ensure that you get the most urgent projects ready for shipping first.”
By standardizing incoming artwork, PrimeCenter minimizes material waste. “Particularly in the DTF market, you see a lot of different artwork workflows coming through,” says Joey, “and not everyone is going to be cautious about your material cost or the time it takes to prepare a project for printing. But what we’re able to do with PrimeCenter is automatically manipulate the file to optimize it for printing. For example, if someone sends me a small logo created on a large art board, PrimeCenter intelligently analyzes the artwork, crops it to the visible content, and adds a normalized offset or padding. It ensures accurate production with no media waste. This will improve the throughput of your printer because you’re cutting down on empty space, and it makes the transfers easier to align and apply to the garment.”
Adding to that, using tear-off annotations increases the workflow accuracy and reduces errors during the application of the transfers.
“We have a number of PrimeCenter DTF customers and this is hands down extremely beneficial to all of them, whether they’re producing transfers for application inhouse or sending them to a third party for application to the garments.” One of the great benefits here is that producing the transfers doesn’t require any kind of complex integration. PrimeCenter uses the file name metadata and can create a tear-off annotation that has a QR code or barcode along with text. “The text can identify the individual file or the order number, but we can also include information on the type of garment in the QR code or the barcode. So if an operator trips and throws all the transfers up into the air, it won’t matter. You still know exactly what garments they need to be married to, which is extremely powerful, especially with multiple workflows.”
Operators can scan the QR code and it will automatically reference the placement of the transfer. Then they can tear off the annotation and put down the heat press, safe in the knowledge that they’ve got the right transfer on the right garment, keeping costs and wastage to a minimum.
PrimeCenter goes with the flow
One of PrimeCenter’s biggest strengths is its agnostic design. It connects seamlessly with any RIP as long as it supports PDFs.
Joey stresses just how important this is: “A lot of DTF companies, and print shops in general, are running multiple printers using different RIP platforms. This means there might be two separate workflows, which is less than ideal in terms of agility and flexibility – it can be really cumbersome. So what I like to emphasize about PrimeCenter is that regardless of what RIP you’re using, you’ll have the same workflow. It can integrate with a number of cutters as well, whether they’re generic PDF, or DXF or HPGL. It also offers some cutter-specific drivers, like for the Secabo DTF cutter, which allows customers to get into cutting for a lower cost with an improved workflow.”
Automate your cutting
DTF printing used to involve operators with a pair of scissors cutting out each transfer by hand, but with today’s ever-increasing volume, this isn’t practical anymore. Instead, using PrimeCenter to automate the job setup, printing and cutting, print shops can be both more efficient and more accurate across the workflow.
According to Joey, “There are a few different ways PrimeCenter can affect multiple departments. Prepress can take in huge batches of files and automatically pass them through PrimeCenter to ensure that they’re effectively nested. It utilizes material as efficiently as possible, as it offers one of the most powerful nesting algorithms on the market, most importantly producing consistent results every time.
“But beyond prepress, looking downstream at finishing, hand-cutting transfers results in several issues. You have to guess where your supposed to cut, so it’s not uncommon for someone to accidentally separate areas of artwork that are meant to stay together, and it also makes it more challenging for the operators to apply the transfers square on the garment. Badly placed transfers lead to errors and material waste.” PrimeCenter can make these issues a thing of the past.
Get started with PrimeCenter
With PrimeCenter’s simple but robust workflow, every department becomes more efficient, contributing time and material savings as well as a more flexible and controllable workflow. Perfect for DTF printshops and for every other area of your print operations.
Interested in PrimeCenter? Click on the link below to book a demo with our workflow specialists!
Subscribe to our Newsletter
Stay in touch with our latest product launches, news and events.